Automation blog
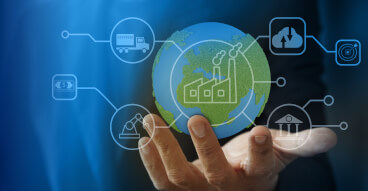
Even if it ain’t broke, you still oughta fix it
04 April, 2024 Making FMCG manufacturing more sustainable through intelligent energy management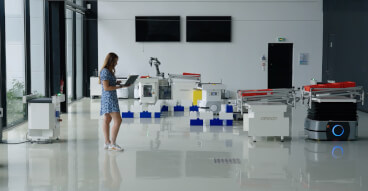
Come on, ladies! Dare to explore exciting career opportunities in automation
01 March, 2024 Maryam Dolatabadi and Asunción Pastrana Costa are experienced automation experts at OMRON. They appeal to girls and women: “Be brave, you are urgently needed in the industry!”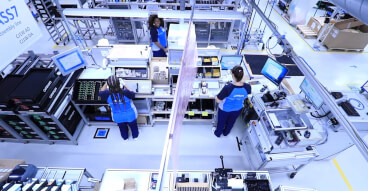
Industrial automation and robotics: still a man’s world?
07 February, 2024 What is it like being a woman in automation today? Three women from OMRON Europe talk about their experiences in the world of industrial automation, the challenges they face, and the tools and support that have helped them to thrive.When Wendy Tonks first started her career in engineering in the UK just over 20 years ago, one of the first ground rules that she had to lay down was that she wasn’t a tea lady.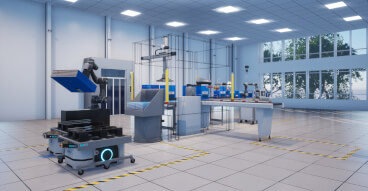
Embracing change: Breaking down the process of flexible manufacturing
30 January, 2024 The fast-moving consumer goods market is experiencing a transformative shift, driven by factors such as consumer empowerment, customization demands, health-conscious preferences, veganism, ethical concerns, and sustainability. We expect that it will undergo more changes in the next decade than it has in the previous 50 years. This necessitates the adaptation of production and supply chains to meet emerging trends. The future of fast-moving consumer goods factories will likely involve smaller, smarter facilities with autonomous movement of goods and interconnected systems.Machines, whether standalone or interconnected, need to be more flexible than ever before to ensure the timely supply of appropriate materials and packaging. Production has to be more agile, increasingly producing retail-ready items with a high mix-low volume approach with zero recalls. The question is how to realize this with minimal cost and fast ROI?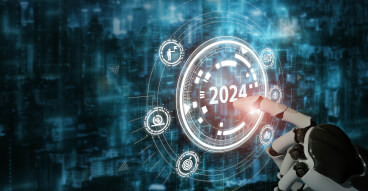
What’s in store for automation in 2024? Six predictions from OMRON Europe
13 December, 2023 The succession of shocks over the last few years has heralded a new era of heightened geopolitical and economic risk. This is prompting manufacturers to build resilience and flexibility into business models and rethink global supply chains and relationships. At the same time, pressure is mounting to incorporate ESG principles into operational decision making. AI, data science, digital twins and sensing, monitoring and vision technology will all be essential to developing automation and control solutions that can help the manufacturing industry adapt to this new reality. In this context, I would like to share the top six trends that will impact and shape industrial automation in 2024 and beyond.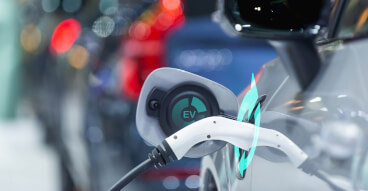
EV transition made easy: Top three challenges to overcome in automotive manufacturing
23 November, 2023 The transition to electric vehicles is a challenging path for automotive manufacturers. Long-established companies that have traditionally produced vehicles with combustion engines are now venturing into an entirely new realm of vehicle platforms. Let us investigate the top challenges facing the electric vehicle manufacturing industry and explore the latest innovative solutions on the horizon.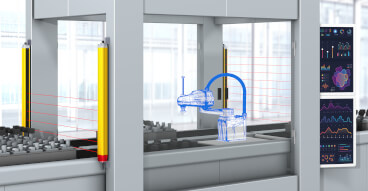
A meeting of minds: IT/OT convergence in industrial automation
22 September, 2023 Future-focused manufacturers are edging closer to their ideals of flexible, efficient and sustainable production by exploring digital transformation in earnest. However, as interest in digitalisation builds, it is becoming apparent that a huge gulf exists between the worlds of OT (Operational Technology) and IT (Information Technology). And this divide needs to be bridged if today’s visions for factories of the future are to become tomorrow’s reality.But before we look at why a convergence of IT and OT is necessary and how this can be achieved, let’s take a step back to basics and clear up some misunderstandings around the terminology.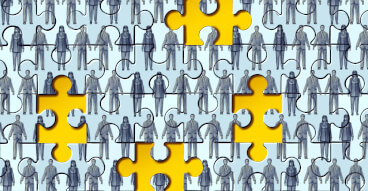
Top 4 Ways to Tackle Labour Shortage with Automation
06 September, 2023 Automation is a pathway to supporting manual workforce and not replacing them.Labour shortages in manufacturing are a growing cause of concern worldwide. While financial incentives and targeted workforce qualifications have been used as countermeasures, more innovative solutions are needed. Many manufacturers choose to automate repetitive activities but to what extent is it supporting the existing taskforce or is it taking away their jobs altogether?In 2023, Reuters disclosed an alarming trend: a record-high 53% of companies grapple with hiring difficulties. Staff shortages, soaring energy costs, combined with the pursuit of climate neutrality create new challenges. In the quest for sustainable manufacturing, innovative strategies to address labour gaps and enhance existing talent are the beacon of progress.Let us go over the top four ways to addressing the labour shortage and supporting the current workforce with automation: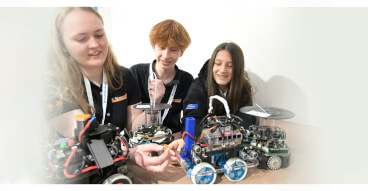
Empowering the workforce: OMRON's approach to skills development in European manufacturing
06 September, 2023 Delving into OMRON's unwavering commitment to nurturing skills that empower the next generation, while the industry embarks on a transformative journey – a journey that unlocks the full potential of the Fourth Industrial Revolution (4IR) while boldly moving towards the Fifth Industrial Revolution (5IR).In the halls of academia, the boardrooms of visionary business leaders, and the chambers of forward-thinking politicians, a fervent debate evokes. It revolves around the profound shift from the Fourth Industrial Revolution, 4IR, or Industry 4.0 as it is also known, to Industry 5.0 will change the world in which we live.Historically the Industrial Revolution was the First Machine Age, and electricity the Second, then electronics was the Third, and the internet as platform the Fourth Machine Age. We are now entering the Fifth Machine Age, which highlights harmonious human-machine collaboration and the contributions of the industry to society. This is the moment to not only adapt but to lead, to pioneer, and to create a future where innovation knows no bounds. Klaus Schwab, the founder and executive chairman of the World Economic Forum has observed that: “We stand on the brink of a technological revolution that will fundamentally alter the way we live, work, and relate to one another. In its scale, scope, and complexity, the transformation will be unlike anything humankind has experienced before. Our world is undergoing a transformative shift. Global production is evolving, driven by the automation of traditional industrial practices through smart technology, M2M communication, and IoT integration. This synergy fuels heightened automation, seamless communication, and intelligent machines that autonomously analyse and diagnose challenges.The rise of AI sparks debates, hinting at deeper transformations within our societal tapestry. As we navigate this dynamic landscape, we are poised to embrace innovation and reshape our future.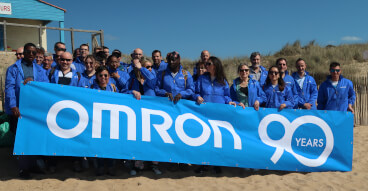
From red lights to robots: OMRON celebrates 90 years of innovation
06 June, 2023 This year on Founder’s Day, OMRON looked back on 90 years of pushing technological boundaries, and looks forward to a future of automation innovation framed by sustainability, digitalisation and human-machine collaboration.May the 10th be with you… Every year, 10th May is probably the most important day in OMRON’s calendar. On this day, 30,000 OMRON employees around the world celebrate the life and legacy of the company’s founder, Kazuma Tateishi. They do this by recommitting to Tateishi’s vision of using technology to create a better world and by giving back to society - often by participating in volunteer and charity projects in their communities. Innovation Milestones OMRON's journey of innovation began in 1933 with the development of a high-precision timer for X-ray photography. This marked the company's first contribution to addressing societal needs. In 1960, OMRON unveiled the world's first non-contact proximity switch, revolutionizing advanced mass production capabilities. Since then, OMRON has continued to introduce groundbreaking technologies, including the first automatic traffic signal, unmanned train station system, wearable blood pressure controller, ultra-high-speed fuzzy logical controller, and automatic cancer cell diagnostic equipment.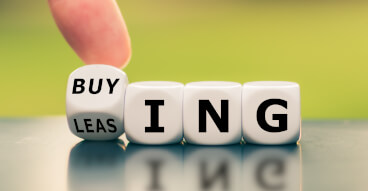
Buying or Leasing? How to finance your new cobot
26 April, 2023 Food for thought for SMEs when funding automation projectsSkills shortages, digitization, sustainability, and energy-saving plans are accelerating automation projects in many companies. Once manual processes that lend themselves to automation have been identified, the next question that usually follows is: And what does it all cost?It can make sense to consider options such as leasing or robot-as-a-service. One example of tools that give small and medium-sized enterprises (SMEs) in particular a better overview the financial aspects of automation is the ROI calculator from OMRON. Anyone currently considering the purchase of a cobot or AMR can use this tool to reveal the return on investment.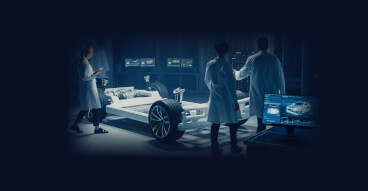
Why automated inspection systems are critical for electric vehicle manufacturing
23 March, 2023 Safety trumps all other concerns in the automotive industry, and electric vehicle manufacturing is no exception. However, safety can also introduce complexity, and the complexity of today’s vehicles – particularly EVs – is such that manufacturers are no longer able to rely on traditional sample or audit-based inspection methods.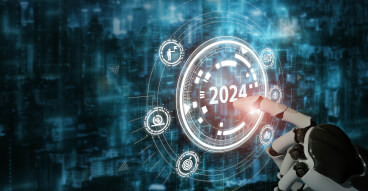
What’s in store for automation in 2024? Six predictions from OMRON Europe
13 December, 2023 The succession of shocks over the last few years has heralded a new era of heightened geopolitical and economic risk. This is prompting manufacturers to build resilience and flexibility into business models and rethink global supply chains and relationships. At the same time, pressure is mounting to incorporate ESG principles into operational decision making. AI, data science, digital twins and sensing, monitoring and vision technology will all be essential to developing automation and control solutions that can help the manufacturing industry adapt to this new reality. In this context, I would like to share the top six trends that will impact and shape industrial automation in 2024 and beyond.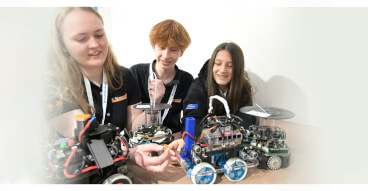
Empowering the workforce: OMRON's approach to skills development in European manufacturing
06 September, 2023 Delving into OMRON's unwavering commitment to nurturing skills that empower the next generation, while the industry embarks on a transformative journey – a journey that unlocks the full potential of the Fourth Industrial Revolution (4IR) while boldly moving towards the Fifth Industrial Revolution (5IR).In the halls of academia, the boardrooms of visionary business leaders, and the chambers of forward-thinking politicians, a fervent debate evokes. It revolves around the profound shift from the Fourth Industrial Revolution, 4IR, or Industry 4.0 as it is also known, to Industry 5.0 will change the world in which we live.Historically the Industrial Revolution was the First Machine Age, and electricity the Second, then electronics was the Third, and the internet as platform the Fourth Machine Age. We are now entering the Fifth Machine Age, which highlights harmonious human-machine collaboration and the contributions of the industry to society. This is the moment to not only adapt but to lead, to pioneer, and to create a future where innovation knows no bounds. Klaus Schwab, the founder and executive chairman of the World Economic Forum has observed that: “We stand on the brink of a technological revolution that will fundamentally alter the way we live, work, and relate to one another. In its scale, scope, and complexity, the transformation will be unlike anything humankind has experienced before. Our world is undergoing a transformative shift. Global production is evolving, driven by the automation of traditional industrial practices through smart technology, M2M communication, and IoT integration. This synergy fuels heightened automation, seamless communication, and intelligent machines that autonomously analyse and diagnose challenges.The rise of AI sparks debates, hinting at deeper transformations within our societal tapestry. As we navigate this dynamic landscape, we are poised to embrace innovation and reshape our future.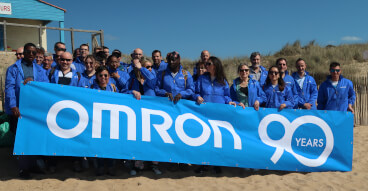
From red lights to robots: OMRON celebrates 90 years of innovation
06 June, 2023 This year on Founder’s Day, OMRON looked back on 90 years of pushing technological boundaries, and looks forward to a future of automation innovation framed by sustainability, digitalisation and human-machine collaboration.May the 10th be with you… Every year, 10th May is probably the most important day in OMRON’s calendar. On this day, 30,000 OMRON employees around the world celebrate the life and legacy of the company’s founder, Kazuma Tateishi. They do this by recommitting to Tateishi’s vision of using technology to create a better world and by giving back to society - often by participating in volunteer and charity projects in their communities. Innovation Milestones OMRON's journey of innovation began in 1933 with the development of a high-precision timer for X-ray photography. This marked the company's first contribution to addressing societal needs. In 1960, OMRON unveiled the world's first non-contact proximity switch, revolutionizing advanced mass production capabilities. Since then, OMRON has continued to introduce groundbreaking technologies, including the first automatic traffic signal, unmanned train station system, wearable blood pressure controller, ultra-high-speed fuzzy logical controller, and automatic cancer cell diagnostic equipment.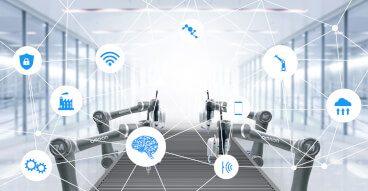
Can Artificial Intelligence (AI) in robot systems manage the functional safety parts?
20 March, 2023 Authors: Josep Plassa, Safety Product Marketing Manager at OMRON Europe and Atsushi Oshiro, Manager at the OMRON Development CenterRobots and AI systems have become an integral part of industrial manufacturing sites. To ensure the safety of workers while using robots, a detailed risk assessment is necessary. This assessment is carried out from the perspective of Functional Safety, which examines the five main elements employed by robots to determine autonomous control actions: Environment recognition, Action planning, Trajectory generation, Motion control, and Measurement.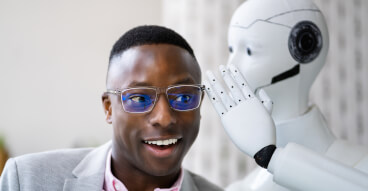
Artificial Intelligence: don’t call me stupid
08 February, 2023 Ten years ago I was quite proud of how smart the machines in our own factory were. Now, with my today’s definition of smart, I realise they were actually quite stupid.Why? Because although they were doing what they were designed to do, the minute they encountered anything unexpected or out of the ordinary they were stumped. They resorted to asking the operator ‘what is wrong with me?’.Troubleshooting and getting machines back up and running called for smart people. Highly skilled operators. Experienced software and hardware engineers. The problem is that in the last ten years, these people have become increasingly unavailable. There quite simply isn’t enough new talent entering the industry to offset the number of workers reaching retirement age. When they leave the business, retirees take with them their hard-earned on-the-job knowledge that is a culmination of years of experience. With each departing worker, businesses are faced with the prospect of a less productive and less skilled workforce.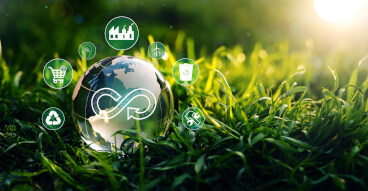
The path to net zero: talking tactics
01 February, 2023 The key to unlocking a net zero future in manufacturing is transforming the value chain through automation.In June 2022, New Scientist reported that a third of the world’s largest companies had net zero targets - significantly more than the same time last year.Whilst it is positive news that momentum is accelerating, the article went on to say that the details of how companies were planning to reach net zero were patchy.Which is not surprising really. Creating and implementing a net zero strategy is a huge undertaking for any business, especially with 80% of GHG emissions falling into Scope 3 - that is emissions that occur upstream or downstream in the value chain. This is a particular challenge for FMCG companies, whose supply chains and onward logistics are long and complex.Most of these businesses know what they need to do: decarbonise and circularise the value chain. And they have a strategy for doing this, which will generally cover: optimising the use of resources and energy, replacing high emission products and processes and eliminating waste.But translating intention into action is where the main challenge lies. This is where automation has a crucial role to play.Data collection and analysis is the key to successful net zero transition. Without it, how do companies know what their starting point is, where they need to improve, whether they have improved and by how much? Robust data is the foundation for turning a commitment into change, and for credibly and confidently communicating with stakeholders and delivering on climate ambitions.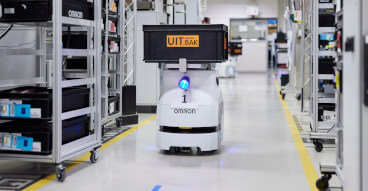
Powering through the energy and fuel crisis with automation
07 December, 2022 To counter rising prices and meet environmental targets, industrial enterprises should explore how automation technologies from a single source might help contribute to their sustainability strategy.High energy and fuel prices are putting a strain on both households and industry. Not only is the situation negatively impacting financial plans and wallets, but the excessive prices are forcing some companies to cease production. According to Make UK 42% of manufacturers surveyed said that their electricity bills have increased by 100% in the past 12 months and 32% said that gas prices have increased by over 100% in the past year. A worrying 12% of manufacturers have already made job cuts as a direct result of increased energy bills.The war in Ukraine, Covid-19 pandemic, and gas pricing are only a few of the causes of the crisis, which impacts all sectors and has an impact on everything from power prices to supply chains. What should manufacturing companies consider now? Comprehensive automation strategies are essential for greater flexibility and energy efficiency. This includes innovative robotics paired with sensor and vision technology as well as artificial intelligence – AI at the Edge. In addition, real-time data from production plants can assist with detecting anomalies and improving overall equipment effectiveness (OEE).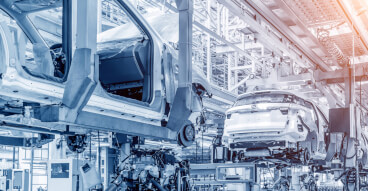
Where is the future heading, intralogistics? Tips for more efficiency
15 November, 2022 Sometimes we focus so much on the big picture that we forget the smaller and yet so important processes that characterize smart production. One example is intralogistics, i.e. the flows of materials and goods that take place on a company's premises or in a production hall. A recent study found that more than 80 percent of the companies surveyed consider the increased use of AI and automation in intralogistics to be necessary to meet challenges such as the shortage of skilled workers or growth plans.Automotive companies that want to meet market and customer requirements, increase efficiency and become more sustainable must come up with new ideas. Energy costs, the gas crisis, and rising inflation make this task even more difficult. Smart factory concepts that combine innovative automation, digitalization, and smart intralogistics approaches can provide valuable support. Some speak of Industry 4.0 in this context, others of the “factory of the future”, still others prefer Industrial Internet of Things (IIoT). But no matter which term you favor: The most important thing is to become active now and to rely on reliable partners. Intralogistics is a good starting point for quickly initiating change. Because action is urgently needed: many companies are currently severely limited due to the shortage of skilled workers. Modern technologies such as mobile robots can provide a remedy.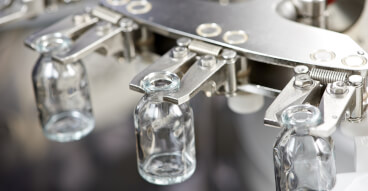
How can adaptive AI inspection contribute to flexible manufacturing?
04 October, 2022 Consumers today demand customized products to meet their personal needs and tastes. Instead of producing items that are ‘made to shelve’ and ‘sent to stock’, manufacturers must personalize products that are ‘made for me’ and ‘sent to me’. This is revolutionizing production and forcing companies to rethink their processes. At the same time, ensuring zero complaints and zero defects is a must.The trained eye of an experienced vision inspector is quick to spot errors, but a routine task like this is tiring, and cannot be carried out at each step of the production, especially due to the current labor shortages in many industries. But could this task be automated also in high-mix low-volume production? Could a smart vision system or an ‘electronic eye’ replicate the discernment of the human eye, with the added benefit of repeatability and robustness? The latest AI-enabled adaptive inspection can overcome the challenges of automated quality inspection, with improved flexibility, productivity, and adaptability.
Artificial Intelligence: hope, hype and FOMO
22 September, 2022 Ten years ago when we received enquiries about AI-based projects, they were mainly driven by hype or FOMO. When I asked why they wanted to get into AI, the answer, more often than not, was either ‘because my boss asked me to’, ‘because we have a lot of data’ or ‘because it seems like an interesting area’. None of these were particularly solid reasons and certainly didn’t justify the hefty investment that AI applications would have required at that time.That is changing, and hope, rather than hype or ‘FOMO’, is the driver. Customers don’t ask whether we can help them with AI anymore. They ask us whether we can help with predictive maintenance, quality control or process optimisation. They come to us with a problem that they want us to help solve. The adoption of AI is no longer a motive or an aim in itself. Instead, AI has become an ‘enabler’.Whatever the industry - whether food & drink, pharmaceutical, electronics or automotive - the end goal is the same: producing high quality, defect-free products at a lower cost, using less energy and less labour. And AI can be one of a suite of solutions for achieving those objectives.
Automation adapts to sustainable packaging
16 August, 2022 Have you ever ordered a small item online, and then felt incensed when it arrived in an oversized box packed out with bubble wrap, air-filled cushions or paper inserts?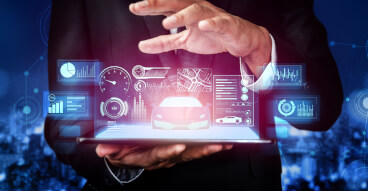
Powering the European automotive industry
29 January, 2021 The European automotive industry is facing strong competition from Asia, as well as the economic challenges of the pandemic. It needs to develop innovative, future-proof strategies and technologies that will boost both efficiency and sustainability. Tony Seba from Stanford University believes that by 2025, no more new vehicles with (pure) combustion engines will be sold and there will be a move towards battery or hydrogen-powered fuel cells. Meanwhile, the industry faces falling sales, increasingly strict emissions regulations, new technologies, digitisation and changing consumer needs. Companies must respond by converting their production lines; becoming more agile; and introducing innovations that provide a competitive edge.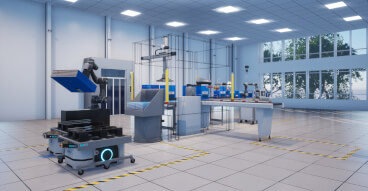
Embracing change: Breaking down the process of flexible manufacturing
30 January, 2024 The fast-moving consumer goods market is experiencing a transformative shift, driven by factors such as consumer empowerment, customization demands, health-conscious preferences, veganism, ethical concerns, and sustainability. We expect that it will undergo more changes in the next decade than it has in the previous 50 years. This necessitates the adaptation of production and supply chains to meet emerging trends. The future of fast-moving consumer goods factories will likely involve smaller, smarter facilities with autonomous movement of goods and interconnected systems.Machines, whether standalone or interconnected, need to be more flexible than ever before to ensure the timely supply of appropriate materials and packaging. Production has to be more agile, increasingly producing retail-ready items with a high mix-low volume approach with zero recalls. The question is how to realize this with minimal cost and fast ROI?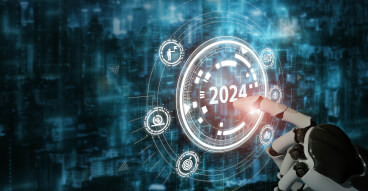
What’s in store for automation in 2024? Six predictions from OMRON Europe
13 December, 2023 The succession of shocks over the last few years has heralded a new era of heightened geopolitical and economic risk. This is prompting manufacturers to build resilience and flexibility into business models and rethink global supply chains and relationships. At the same time, pressure is mounting to incorporate ESG principles into operational decision making. AI, data science, digital twins and sensing, monitoring and vision technology will all be essential to developing automation and control solutions that can help the manufacturing industry adapt to this new reality. In this context, I would like to share the top six trends that will impact and shape industrial automation in 2024 and beyond.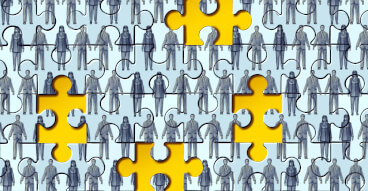
Top 4 Ways to Tackle Labour Shortage with Automation
06 September, 2023 Automation is a pathway to supporting manual workforce and not replacing them.Labour shortages in manufacturing are a growing cause of concern worldwide. While financial incentives and targeted workforce qualifications have been used as countermeasures, more innovative solutions are needed. Many manufacturers choose to automate repetitive activities but to what extent is it supporting the existing taskforce or is it taking away their jobs altogether?In 2023, Reuters disclosed an alarming trend: a record-high 53% of companies grapple with hiring difficulties. Staff shortages, soaring energy costs, combined with the pursuit of climate neutrality create new challenges. In the quest for sustainable manufacturing, innovative strategies to address labour gaps and enhance existing talent are the beacon of progress.Let us go over the top four ways to addressing the labour shortage and supporting the current workforce with automation: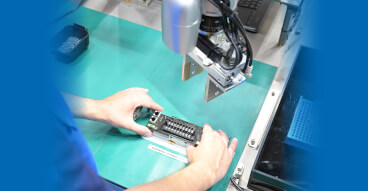
Top 5 automation predictions for 2023 from OMRON Europe
01 February, 2023 While a new year is upon us, with all its opportunities, I'd like to highlight some of the top trends that will impact and shape industrial automation in 2023 and beyond. The manufacturing industries will continue to face many challenges, and riding them out will involve building resilience and flexibility into business models. At the same time, companies must embrace emerging technologies - sensing, robotics, 5G and artificial intelligence - to help them solve the problems they face due to societal challenges.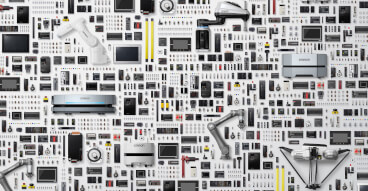
Riders of the storm: navigating economic uncertainty by turning social challenges into tech opportunities
06 December, 2022 One of the questions I am often asked is what our strategy is, as an industrial automation business, for maintaining stable growth in a volatile and increasingly unpredictable global economy. My answer, as you might imagine, is not one sentence, although it is rooted in one concept: SINIC. SINIC stands for ‘Seed-Innovation to Need-Impetus Cyclic Evolution’ and is a theory that was developed by OMRON's founder, Dr. Kazuma Tateisi, in 1970. According to this philosophy, science, technology and society share a cyclical relationship, mutually impacting and influencing each other. Scientific breakthroughs help society to advance and social needs spur on technological development. OMRON Europe has always followed this philosophy, and has spent the last decade laying the foundations for creating value-adding solutions to present day social and economic challenges.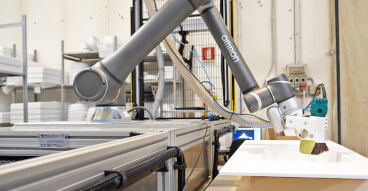
Four Automation Tips for SMEs
25 November, 2022 Corporate leaders around the world are currently facing one challenge after another: In addition to the exploding costs caused by the energy crisis, there are supply chain problems, a shortage of skilled workers, sustainability requirements, and advancing digitization issues. In particular, small and medium-sized enterprises (SME) need to quickly find ways to address these hurdles. Automation provides a remedy – this includes robotics such as cobots and AMR (autonomous mobile robots), as well as sensors, vision, and AI technology. While companies are well aware of the benefits of such technologies, studies also show that many remain skeptical of their actual use.Especially companies without application experience fear that the use of robots could be accompanied by high costs. So if you are currently wondering whether the purchase of a collaborative or mobile robot is worthwhile for your own business, OMRON's new ROI calculator will help. It provides a quick overview of the return on investment and shows when a robotics investment will cover its costs.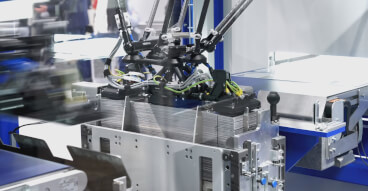
Digitalization in the automotive industry: Seven tips for smart production
02 November, 2022 If you want to grow and master crises, you have to be digitally fit – this also applies to the important automotive sector. There is no way around digital tools for addressing customers or productivity. Artificial intelligence (AI) and sustainability are key drivers and focus topics, as a study by Capgemini shows. Experts from Gartner point out the importance of open-source collaboration approaches, holistic ecosystems, and technology partnerships. But what should we look out for in digitalization and intralogistics in the production of the future? We want to answer this question in two parts. We start with tips on digitization in the smart factory. As an automation expert, OMRON has been accompanying manufacturers and suppliers on their way to more digitalization sophistication for many years.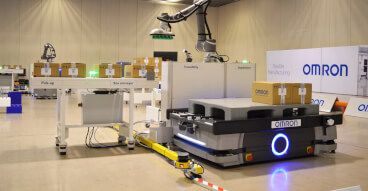
Flexible Manufacturing Roadshow: Taking the factory of the future across Europe
16 June, 2022 What if you could see, feel and touch the factory of the future? What does it take to realize flexible, efficient, and sustainable production? This is the idea behind OMRON’s unique Flexible Manufacturing Roadshow travelling across Europe this year. The roadshow features exclusive demonstrations of human-machine collaborative solutions not usually seen outside of a factory setting due to their size and scale.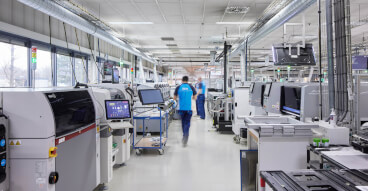
Building the Factory of the Future together
16 June, 2022 As one of the largest business units at OMRON, we aim to further develop the Den Bosch plant to serve the needs in the EMEA region.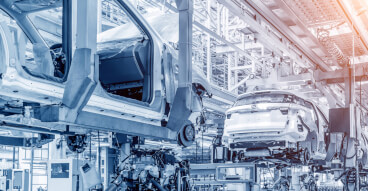
Traceability in Automotive: What decision-makers and experts should look out for now
23 May, 2022 From e-mobility to autonomous driving, from skills shortages to digitalization: The automotive industry is undergoing a profound change, marked, for example, by a shift to globalized platforms and standardized vehicle architectures. On the one hand, production is becoming increasingly efficient, but on the other, even a single faulty part can have more far-reaching effects than ever before. Faced with costly recalls, automotive manufacturers are confronted with increasingly complex requirements and stricter specifications. Is the effort of traceability worth it if it means labeling up to 20,000 parts per vehicle? Yes, it is, but powerful reading and verification technologies along with powerful software is needed to make sense of all the data.There are several reasons why manufacturers need to keep accurate records of the parts and components that make up a new car. From a quality perspective, for example, barcode tracking helps to ensure that the right parts are put together. Even more important, however, is the ability to trace each car part back to its original supplier. In the event of a recall or the discovery of a faulty part, manufacturers have to be able to quickly and comprehensively find out where each part came from. This is complemented by information such as batch number, date of manufacture and other important information to identify which vehicles are affected by a defective part. Recommendations and standards from AIAG, VDA, ANSI and ISO specify the details. As the automotive industry globalizes, worldwide production of light vehicles is expected to reach around 96 million units by 2023. This means that even a single faulty part can have an enormous impact, and therefore must be prevented at all costs.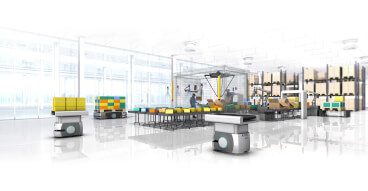
Mastering packaging and intralogistics challenges in eCommerce
24 February, 2022 Robot-assisted packaging enables fast and cost-efficient scalability upward and downward to handle swings in demands from the supply chain.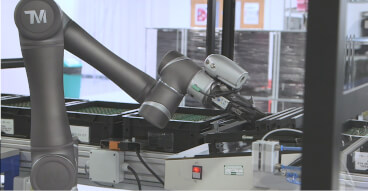
Hanover Displays automates PCBA testing with cobots
31 January, 2022 UK-based Hanover Displays Limited needed a new system for testing printed circuit board assemblies (PCBAs) and selected OMRON TM cobots for the job, supplied and installed by Absolute Robotics, part of the Absolute Automation Group.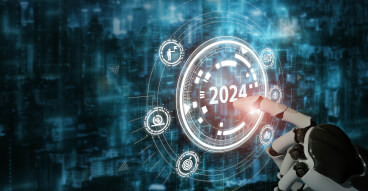
What’s in store for automation in 2024? Six predictions from OMRON Europe
13 December, 2023 The succession of shocks over the last few years has heralded a new era of heightened geopolitical and economic risk. This is prompting manufacturers to build resilience and flexibility into business models and rethink global supply chains and relationships. At the same time, pressure is mounting to incorporate ESG principles into operational decision making. AI, data science, digital twins and sensing, monitoring and vision technology will all be essential to developing automation and control solutions that can help the manufacturing industry adapt to this new reality. In this context, I would like to share the top six trends that will impact and shape industrial automation in 2024 and beyond.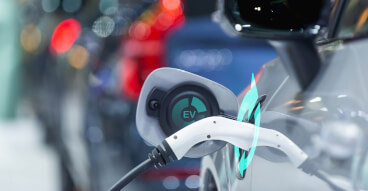
EV transition made easy: Top three challenges to overcome in automotive manufacturing
23 November, 2023 The transition to electric vehicles is a challenging path for automotive manufacturers. Long-established companies that have traditionally produced vehicles with combustion engines are now venturing into an entirely new realm of vehicle platforms. Let us investigate the top challenges facing the electric vehicle manufacturing industry and explore the latest innovative solutions on the horizon.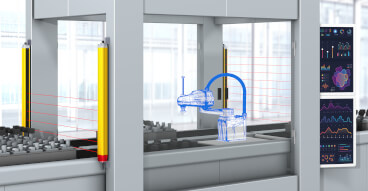
A meeting of minds: IT/OT convergence in industrial automation
22 September, 2023 Future-focused manufacturers are edging closer to their ideals of flexible, efficient and sustainable production by exploring digital transformation in earnest. However, as interest in digitalisation builds, it is becoming apparent that a huge gulf exists between the worlds of OT (Operational Technology) and IT (Information Technology). And this divide needs to be bridged if today’s visions for factories of the future are to become tomorrow’s reality.But before we look at why a convergence of IT and OT is necessary and how this can be achieved, let’s take a step back to basics and clear up some misunderstandings around the terminology.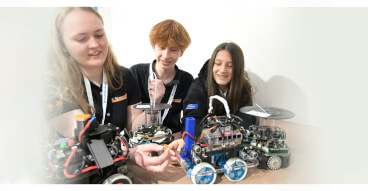
Empowering the workforce: OMRON's approach to skills development in European manufacturing
06 September, 2023 Delving into OMRON's unwavering commitment to nurturing skills that empower the next generation, while the industry embarks on a transformative journey – a journey that unlocks the full potential of the Fourth Industrial Revolution (4IR) while boldly moving towards the Fifth Industrial Revolution (5IR).In the halls of academia, the boardrooms of visionary business leaders, and the chambers of forward-thinking politicians, a fervent debate evokes. It revolves around the profound shift from the Fourth Industrial Revolution, 4IR, or Industry 4.0 as it is also known, to Industry 5.0 will change the world in which we live.Historically the Industrial Revolution was the First Machine Age, and electricity the Second, then electronics was the Third, and the internet as platform the Fourth Machine Age. We are now entering the Fifth Machine Age, which highlights harmonious human-machine collaboration and the contributions of the industry to society. This is the moment to not only adapt but to lead, to pioneer, and to create a future where innovation knows no bounds. Klaus Schwab, the founder and executive chairman of the World Economic Forum has observed that: “We stand on the brink of a technological revolution that will fundamentally alter the way we live, work, and relate to one another. In its scale, scope, and complexity, the transformation will be unlike anything humankind has experienced before. Our world is undergoing a transformative shift. Global production is evolving, driven by the automation of traditional industrial practices through smart technology, M2M communication, and IoT integration. This synergy fuels heightened automation, seamless communication, and intelligent machines that autonomously analyse and diagnose challenges.The rise of AI sparks debates, hinting at deeper transformations within our societal tapestry. As we navigate this dynamic landscape, we are poised to embrace innovation and reshape our future.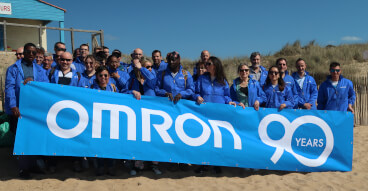
From red lights to robots: OMRON celebrates 90 years of innovation
06 June, 2023 This year on Founder’s Day, OMRON looked back on 90 years of pushing technological boundaries, and looks forward to a future of automation innovation framed by sustainability, digitalisation and human-machine collaboration.May the 10th be with you… Every year, 10th May is probably the most important day in OMRON’s calendar. On this day, 30,000 OMRON employees around the world celebrate the life and legacy of the company’s founder, Kazuma Tateishi. They do this by recommitting to Tateishi’s vision of using technology to create a better world and by giving back to society - often by participating in volunteer and charity projects in their communities. Innovation Milestones OMRON's journey of innovation began in 1933 with the development of a high-precision timer for X-ray photography. This marked the company's first contribution to addressing societal needs. In 1960, OMRON unveiled the world's first non-contact proximity switch, revolutionizing advanced mass production capabilities. Since then, OMRON has continued to introduce groundbreaking technologies, including the first automatic traffic signal, unmanned train station system, wearable blood pressure controller, ultra-high-speed fuzzy logical controller, and automatic cancer cell diagnostic equipment.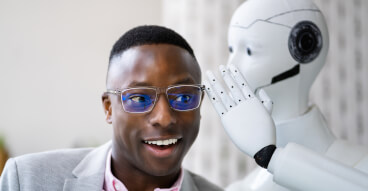
Artificial Intelligence: don’t call me stupid
08 February, 2023 Ten years ago I was quite proud of how smart the machines in our own factory were. Now, with my today’s definition of smart, I realise they were actually quite stupid.Why? Because although they were doing what they were designed to do, the minute they encountered anything unexpected or out of the ordinary they were stumped. They resorted to asking the operator ‘what is wrong with me?’.Troubleshooting and getting machines back up and running called for smart people. Highly skilled operators. Experienced software and hardware engineers. The problem is that in the last ten years, these people have become increasingly unavailable. There quite simply isn’t enough new talent entering the industry to offset the number of workers reaching retirement age. When they leave the business, retirees take with them their hard-earned on-the-job knowledge that is a culmination of years of experience. With each departing worker, businesses are faced with the prospect of a less productive and less skilled workforce.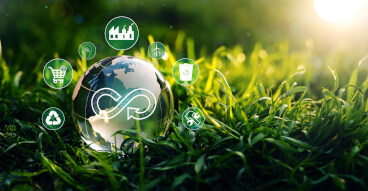
The path to net zero: talking tactics
01 February, 2023 The key to unlocking a net zero future in manufacturing is transforming the value chain through automation.In June 2022, New Scientist reported that a third of the world’s largest companies had net zero targets - significantly more than the same time last year.Whilst it is positive news that momentum is accelerating, the article went on to say that the details of how companies were planning to reach net zero were patchy.Which is not surprising really. Creating and implementing a net zero strategy is a huge undertaking for any business, especially with 80% of GHG emissions falling into Scope 3 - that is emissions that occur upstream or downstream in the value chain. This is a particular challenge for FMCG companies, whose supply chains and onward logistics are long and complex.Most of these businesses know what they need to do: decarbonise and circularise the value chain. And they have a strategy for doing this, which will generally cover: optimising the use of resources and energy, replacing high emission products and processes and eliminating waste.But translating intention into action is where the main challenge lies. This is where automation has a crucial role to play.Data collection and analysis is the key to successful net zero transition. Without it, how do companies know what their starting point is, where they need to improve, whether they have improved and by how much? Robust data is the foundation for turning a commitment into change, and for credibly and confidently communicating with stakeholders and delivering on climate ambitions.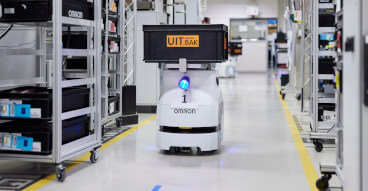
Powering through the energy and fuel crisis with automation
07 December, 2022 To counter rising prices and meet environmental targets, industrial enterprises should explore how automation technologies from a single source might help contribute to their sustainability strategy.High energy and fuel prices are putting a strain on both households and industry. Not only is the situation negatively impacting financial plans and wallets, but the excessive prices are forcing some companies to cease production. According to Make UK 42% of manufacturers surveyed said that their electricity bills have increased by 100% in the past 12 months and 32% said that gas prices have increased by over 100% in the past year. A worrying 12% of manufacturers have already made job cuts as a direct result of increased energy bills.The war in Ukraine, Covid-19 pandemic, and gas pricing are only a few of the causes of the crisis, which impacts all sectors and has an impact on everything from power prices to supply chains. What should manufacturing companies consider now? Comprehensive automation strategies are essential for greater flexibility and energy efficiency. This includes innovative robotics paired with sensor and vision technology as well as artificial intelligence – AI at the Edge. In addition, real-time data from production plants can assist with detecting anomalies and improving overall equipment effectiveness (OEE).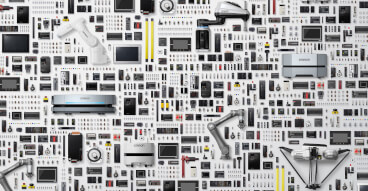
Riders of the storm: navigating economic uncertainty by turning social challenges into tech opportunities
06 December, 2022 One of the questions I am often asked is what our strategy is, as an industrial automation business, for maintaining stable growth in a volatile and increasingly unpredictable global economy. My answer, as you might imagine, is not one sentence, although it is rooted in one concept: SINIC. SINIC stands for ‘Seed-Innovation to Need-Impetus Cyclic Evolution’ and is a theory that was developed by OMRON's founder, Dr. Kazuma Tateisi, in 1970. According to this philosophy, science, technology and society share a cyclical relationship, mutually impacting and influencing each other. Scientific breakthroughs help society to advance and social needs spur on technological development. OMRON Europe has always followed this philosophy, and has spent the last decade laying the foundations for creating value-adding solutions to present day social and economic challenges.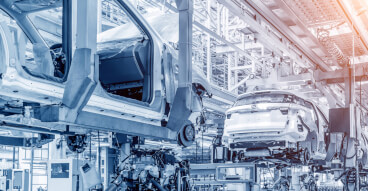
Where is the future heading, intralogistics? Tips for more efficiency
15 November, 2022 Sometimes we focus so much on the big picture that we forget the smaller and yet so important processes that characterize smart production. One example is intralogistics, i.e. the flows of materials and goods that take place on a company's premises or in a production hall. A recent study found that more than 80 percent of the companies surveyed consider the increased use of AI and automation in intralogistics to be necessary to meet challenges such as the shortage of skilled workers or growth plans.Automotive companies that want to meet market and customer requirements, increase efficiency and become more sustainable must come up with new ideas. Energy costs, the gas crisis, and rising inflation make this task even more difficult. Smart factory concepts that combine innovative automation, digitalization, and smart intralogistics approaches can provide valuable support. Some speak of Industry 4.0 in this context, others of the “factory of the future”, still others prefer Industrial Internet of Things (IIoT). But no matter which term you favor: The most important thing is to become active now and to rely on reliable partners. Intralogistics is a good starting point for quickly initiating change. Because action is urgently needed: many companies are currently severely limited due to the shortage of skilled workers. Modern technologies such as mobile robots can provide a remedy.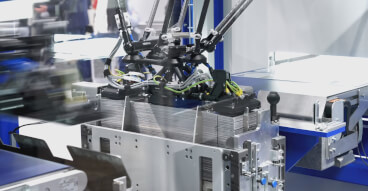
Digitalization in the automotive industry: Seven tips for smart production
02 November, 2022 If you want to grow and master crises, you have to be digitally fit – this also applies to the important automotive sector. There is no way around digital tools for addressing customers or productivity. Artificial intelligence (AI) and sustainability are key drivers and focus topics, as a study by Capgemini shows. Experts from Gartner point out the importance of open-source collaboration approaches, holistic ecosystems, and technology partnerships. But what should we look out for in digitalization and intralogistics in the production of the future? We want to answer this question in two parts. We start with tips on digitization in the smart factory. As an automation expert, OMRON has been accompanying manufacturers and suppliers on their way to more digitalization sophistication for many years.
Artificial Intelligence: hope, hype and FOMO
22 September, 2022 Ten years ago when we received enquiries about AI-based projects, they were mainly driven by hype or FOMO. When I asked why they wanted to get into AI, the answer, more often than not, was either ‘because my boss asked me to’, ‘because we have a lot of data’ or ‘because it seems like an interesting area’. None of these were particularly solid reasons and certainly didn’t justify the hefty investment that AI applications would have required at that time.That is changing, and hope, rather than hype or ‘FOMO’, is the driver. Customers don’t ask whether we can help them with AI anymore. They ask us whether we can help with predictive maintenance, quality control or process optimisation. They come to us with a problem that they want us to help solve. The adoption of AI is no longer a motive or an aim in itself. Instead, AI has become an ‘enabler’.Whatever the industry - whether food & drink, pharmaceutical, electronics or automotive - the end goal is the same: producing high quality, defect-free products at a lower cost, using less energy and less labour. And AI can be one of a suite of solutions for achieving those objectives.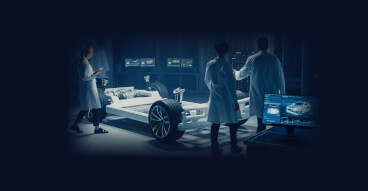
Why automated inspection systems are critical for electric vehicle manufacturing
23 March, 2023 Safety trumps all other concerns in the automotive industry, and electric vehicle manufacturing is no exception. However, safety can also introduce complexity, and the complexity of today’s vehicles – particularly EVs – is such that manufacturers are no longer able to rely on traditional sample or audit-based inspection methods.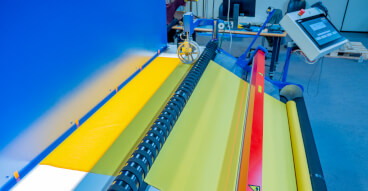
Vadain automates the inspection of curtain fabrics with machine vision
08 April, 2022 Vadain, the market leader in custom curtains in the Netherlands, needed a solution to detect errors as early as possible in kilometers of curtain fabrics. Together with software developers from Sycade, OMRON machine vision technology, and machine builder Eisenkolb, they developed an automated solution to detect and analyze errors in curtain fabrics, making the time-consuming manual inspection process a thing of the past.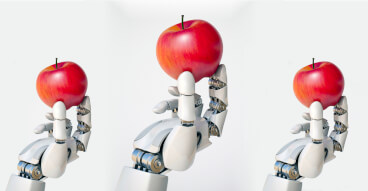
Factory automation: four tips for the future of food & beverage manufacturing
16 July, 2020 The coronavirus pandemic has posed major challenges to organisations of all types and sizes. In the food and commodity industry, companies have faced significantly reduced consumption and disrupted supply chains, while at-home consumption increased, and out-of-home consumption came near to a standstill. But how can manufacturers adapt their business strategies and production processes both now and in the longer term? The pandemic may provide an opportunity for rethinking outdated processes and procedures and enhancing them with concepts such as innovative robotics, sensor technology and holistic automation strategies.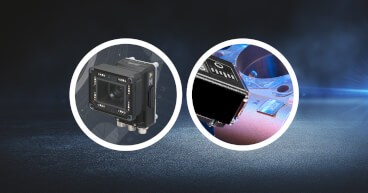
Six challenges for brand protection
19 November, 2019 Brand protection is an important topic for any business. But as industrial companies invest in new technology, such as smart robotics, artificial intelligence and vision systems, are they aware of the key challenges that could affect their brand?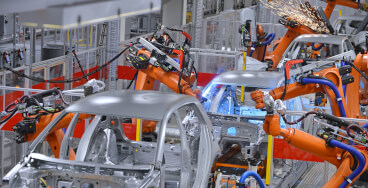
Legacy of machine vision
16 October, 2019 Did you know that for more than 40 years, Omron has developed vision sensing technologies for factory automation, surveillance and transport systems, and more recently for facial recognition and image processing for mobile phones, and even driver monitoring for autonomous driving?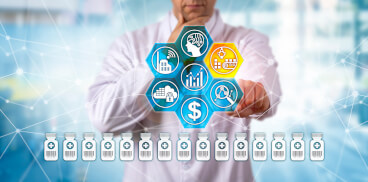
Late-stage customization in pharmaceutical manufacturing
16 October, 2019 As a result of serialization legislation, pharmaceutical manufacturers must now ensure that labels printed at a late stage contain all of the data required for compliance. This includes customizing product labels for certain markets, customers or products by adding variable data to labels or packaging. This avoids the need to stock individual packaging materials for each variant.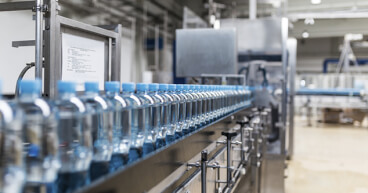
How to secure FMCG supply chains with traceability?
02 October, 2019 The traceability of food and drink products throughout the production and distribution process can be a complex issue. For example, alcoholic drink producers need systems that enable them to comply with local regulations regarding food traceability, as well as tax legislation.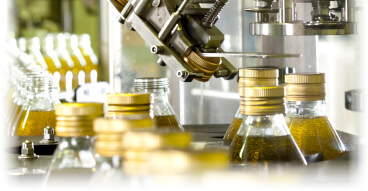
Barcodes: keeping track of product quality
02 October, 2019 For many years, barcode technology has proved to be an economical and flexible identification technology. It has continued to develop and as a result, 1D and 2D codes (such as Datamatrix) are now used almost universally. Their versatility have made them a popular choice for streamlining many key supply chain processes, including production, logistics and item traceability.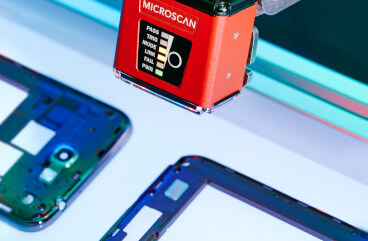
Is your production line ready for inspection?
12 September, 2019 Quality inspections are a critical requirement for all manufacturing and packaging lines. Being able to identify defective products before they are shipped to customers can bring significant savings in both time and money. It prevents costly product recalls, wasted production and potentially expensive legal costs.For perishable products – from food to pharmaceuticals – quality inspection of the packaging is also vital. An unreadable barcode or a wrong expiry date could lead to perfectly good products being discarded. And increasingly strict legislation is making clear marking a top priority for all types of products.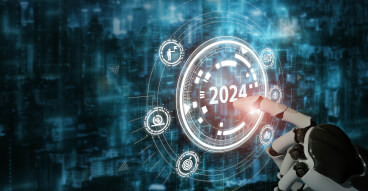
What’s in store for automation in 2024? Six predictions from OMRON Europe
13 December, 2023 The succession of shocks over the last few years has heralded a new era of heightened geopolitical and economic risk. This is prompting manufacturers to build resilience and flexibility into business models and rethink global supply chains and relationships. At the same time, pressure is mounting to incorporate ESG principles into operational decision making. AI, data science, digital twins and sensing, monitoring and vision technology will all be essential to developing automation and control solutions that can help the manufacturing industry adapt to this new reality. In this context, I would like to share the top six trends that will impact and shape industrial automation in 2024 and beyond.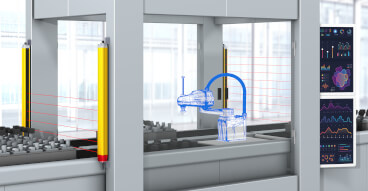
A meeting of minds: IT/OT convergence in industrial automation
22 September, 2023 Future-focused manufacturers are edging closer to their ideals of flexible, efficient and sustainable production by exploring digital transformation in earnest. However, as interest in digitalisation builds, it is becoming apparent that a huge gulf exists between the worlds of OT (Operational Technology) and IT (Information Technology). And this divide needs to be bridged if today’s visions for factories of the future are to become tomorrow’s reality.But before we look at why a convergence of IT and OT is necessary and how this can be achieved, let’s take a step back to basics and clear up some misunderstandings around the terminology.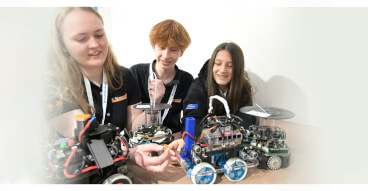
Empowering the workforce: OMRON's approach to skills development in European manufacturing
06 September, 2023 Delving into OMRON's unwavering commitment to nurturing skills that empower the next generation, while the industry embarks on a transformative journey – a journey that unlocks the full potential of the Fourth Industrial Revolution (4IR) while boldly moving towards the Fifth Industrial Revolution (5IR).In the halls of academia, the boardrooms of visionary business leaders, and the chambers of forward-thinking politicians, a fervent debate evokes. It revolves around the profound shift from the Fourth Industrial Revolution, 4IR, or Industry 4.0 as it is also known, to Industry 5.0 will change the world in which we live.Historically the Industrial Revolution was the First Machine Age, and electricity the Second, then electronics was the Third, and the internet as platform the Fourth Machine Age. We are now entering the Fifth Machine Age, which highlights harmonious human-machine collaboration and the contributions of the industry to society. This is the moment to not only adapt but to lead, to pioneer, and to create a future where innovation knows no bounds. Klaus Schwab, the founder and executive chairman of the World Economic Forum has observed that: “We stand on the brink of a technological revolution that will fundamentally alter the way we live, work, and relate to one another. In its scale, scope, and complexity, the transformation will be unlike anything humankind has experienced before. Our world is undergoing a transformative shift. Global production is evolving, driven by the automation of traditional industrial practices through smart technology, M2M communication, and IoT integration. This synergy fuels heightened automation, seamless communication, and intelligent machines that autonomously analyse and diagnose challenges.The rise of AI sparks debates, hinting at deeper transformations within our societal tapestry. As we navigate this dynamic landscape, we are poised to embrace innovation and reshape our future.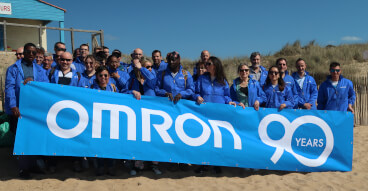
From red lights to robots: OMRON celebrates 90 years of innovation
06 June, 2023 This year on Founder’s Day, OMRON looked back on 90 years of pushing technological boundaries, and looks forward to a future of automation innovation framed by sustainability, digitalisation and human-machine collaboration.May the 10th be with you… Every year, 10th May is probably the most important day in OMRON’s calendar. On this day, 30,000 OMRON employees around the world celebrate the life and legacy of the company’s founder, Kazuma Tateishi. They do this by recommitting to Tateishi’s vision of using technology to create a better world and by giving back to society - often by participating in volunteer and charity projects in their communities. Innovation Milestones OMRON's journey of innovation began in 1933 with the development of a high-precision timer for X-ray photography. This marked the company's first contribution to addressing societal needs. In 1960, OMRON unveiled the world's first non-contact proximity switch, revolutionizing advanced mass production capabilities. Since then, OMRON has continued to introduce groundbreaking technologies, including the first automatic traffic signal, unmanned train station system, wearable blood pressure controller, ultra-high-speed fuzzy logical controller, and automatic cancer cell diagnostic equipment.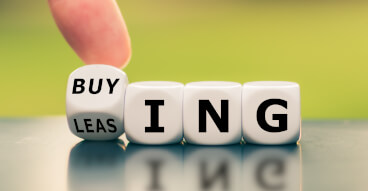
Buying or Leasing? How to finance your new cobot
26 April, 2023 Food for thought for SMEs when funding automation projectsSkills shortages, digitization, sustainability, and energy-saving plans are accelerating automation projects in many companies. Once manual processes that lend themselves to automation have been identified, the next question that usually follows is: And what does it all cost?It can make sense to consider options such as leasing or robot-as-a-service. One example of tools that give small and medium-sized enterprises (SMEs) in particular a better overview the financial aspects of automation is the ROI calculator from OMRON. Anyone currently considering the purchase of a cobot or AMR can use this tool to reveal the return on investment.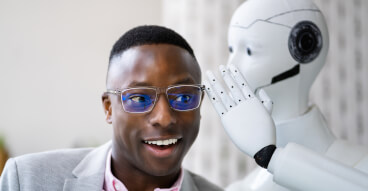
Artificial Intelligence: don’t call me stupid
08 February, 2023 Ten years ago I was quite proud of how smart the machines in our own factory were. Now, with my today’s definition of smart, I realise they were actually quite stupid.Why? Because although they were doing what they were designed to do, the minute they encountered anything unexpected or out of the ordinary they were stumped. They resorted to asking the operator ‘what is wrong with me?’.Troubleshooting and getting machines back up and running called for smart people. Highly skilled operators. Experienced software and hardware engineers. The problem is that in the last ten years, these people have become increasingly unavailable. There quite simply isn’t enough new talent entering the industry to offset the number of workers reaching retirement age. When they leave the business, retirees take with them their hard-earned on-the-job knowledge that is a culmination of years of experience. With each departing worker, businesses are faced with the prospect of a less productive and less skilled workforce.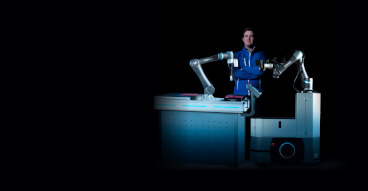
How to speed up cobot integration
08 February, 2023 Good planning and strong partners help SMEs overcome hurdles in automation.Collaborative robots, also known as cobots, are enjoying great popularity because they make it possible to automate time-consuming and resource-intensive tasks. The global market for collaborative robots is currently estimated at around $1.2 billion. The sales volume of cobots reached a total of 32,300 units in 2021. Especially in times when it is becoming increasingly difficult for companies to find and retain suitable employees, such technologies are worth their weight in gold in many places. Speaking of gold, some may ask: Cobots must be extremely expensive, right? When does such an investment pay off?Automation expert OMRON would like to alleviate such worries, especially for small and medium-sized companies: Smart and integrated robotics solutions as well as cobots and mobile robots are feasible and affordable. For those who want to estimate the return on investment, OMRON’s ROI calculator provides a quick and easy overview.Cobots and autonomous mobile robots (AMR) are suitable for both SMEs and large-scale businesses. They perform tasks such as transport, palletizing, loading and unloading of machines, assembly, painting, or welding. They can be quickly and flexibly retooled and also programmed by non-experts. Material replenishment can be streamlined with AMRs, and machine and process loading with cobots. However, to successfully carry out such projects and accelerate robot integration, know-how and partners who are familiar with the subject matter are needed. And above all, employees must be informed and involved from the start of the project to be part of the change together.Here are some tips companies should keep in mind when integrating cobots: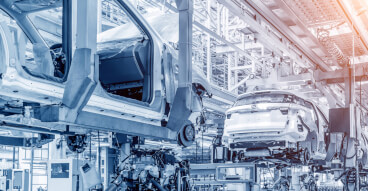
Where is the future heading, intralogistics? Tips for more efficiency
15 November, 2022 Sometimes we focus so much on the big picture that we forget the smaller and yet so important processes that characterize smart production. One example is intralogistics, i.e. the flows of materials and goods that take place on a company's premises or in a production hall. A recent study found that more than 80 percent of the companies surveyed consider the increased use of AI and automation in intralogistics to be necessary to meet challenges such as the shortage of skilled workers or growth plans.Automotive companies that want to meet market and customer requirements, increase efficiency and become more sustainable must come up with new ideas. Energy costs, the gas crisis, and rising inflation make this task even more difficult. Smart factory concepts that combine innovative automation, digitalization, and smart intralogistics approaches can provide valuable support. Some speak of Industry 4.0 in this context, others of the “factory of the future”, still others prefer Industrial Internet of Things (IIoT). But no matter which term you favor: The most important thing is to become active now and to rely on reliable partners. Intralogistics is a good starting point for quickly initiating change. Because action is urgently needed: many companies are currently severely limited due to the shortage of skilled workers. Modern technologies such as mobile robots can provide a remedy.
Artificial Intelligence: hope, hype and FOMO
22 September, 2022 Ten years ago when we received enquiries about AI-based projects, they were mainly driven by hype or FOMO. When I asked why they wanted to get into AI, the answer, more often than not, was either ‘because my boss asked me to’, ‘because we have a lot of data’ or ‘because it seems like an interesting area’. None of these were particularly solid reasons and certainly didn’t justify the hefty investment that AI applications would have required at that time.That is changing, and hope, rather than hype or ‘FOMO’, is the driver. Customers don’t ask whether we can help them with AI anymore. They ask us whether we can help with predictive maintenance, quality control or process optimisation. They come to us with a problem that they want us to help solve. The adoption of AI is no longer a motive or an aim in itself. Instead, AI has become an ‘enabler’.Whatever the industry - whether food & drink, pharmaceutical, electronics or automotive - the end goal is the same: producing high quality, defect-free products at a lower cost, using less energy and less labour. And AI can be one of a suite of solutions for achieving those objectives.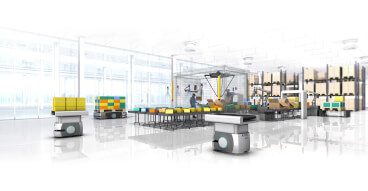
Mastering packaging and intralogistics challenges in eCommerce
24 February, 2022 Robot-assisted packaging enables fast and cost-efficient scalability upward and downward to handle swings in demands from the supply chain.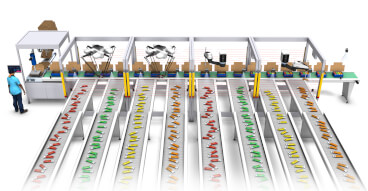
Five challenges in High-Mix, Low-Volume (HMLV) packaging and palletizing processes
21 December, 2021 The new product has just left the factory, in a shelf-ready package in the specified mixed ratio to meet customer needs. The packaging has actually been handled by another company: a co-packer. Co-packing can be found in all Fast-Moving Consumer Goods (FMCG) markets, but especially in the higher-priced product segments such as personal care or confectionery, to name a few examples. It is a fast-growing activity to satisfy the consumer demand for more variety.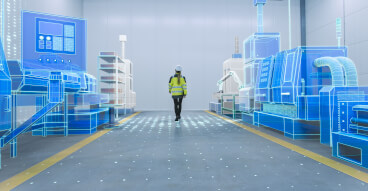
Productivity Peaks: Moving Maintenance From Preventive to Predictive
17 December, 2021 Maintenance is a vital key to a thriving business, especially in manufacturing where 24/7 plant equipment uptime is often expected as standard. As any established enterprise knows, keeping production lines and systems running optimally requires more than a skilled maintenance team. It also involves careful planning, tight scheduling, constant vigilance, a willingness to change out unworn parts, and a readiness to respond to unplanned events. At least, it used to.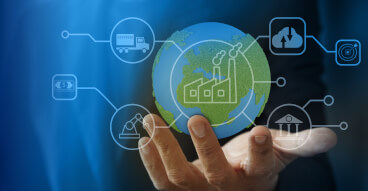
Even if it ain’t broke, you still oughta fix it
04 April, 2024 Making FMCG manufacturing more sustainable through intelligent energy management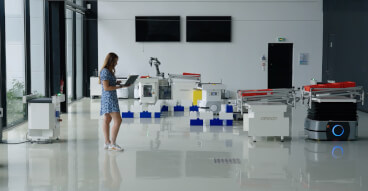
Come on, ladies! Dare to explore exciting career opportunities in automation
01 March, 2024 Maryam Dolatabadi and Asunción Pastrana Costa are experienced automation experts at OMRON. They appeal to girls and women: “Be brave, you are urgently needed in the industry!”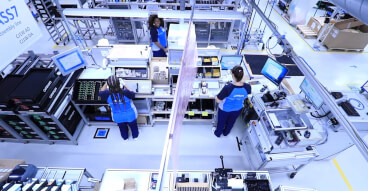
Industrial automation and robotics: still a man’s world?
07 February, 2024 What is it like being a woman in automation today? Three women from OMRON Europe talk about their experiences in the world of industrial automation, the challenges they face, and the tools and support that have helped them to thrive.When Wendy Tonks first started her career in engineering in the UK just over 20 years ago, one of the first ground rules that she had to lay down was that she wasn’t a tea lady.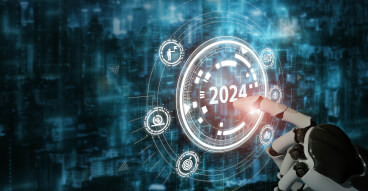
What’s in store for automation in 2024? Six predictions from OMRON Europe
13 December, 2023 The succession of shocks over the last few years has heralded a new era of heightened geopolitical and economic risk. This is prompting manufacturers to build resilience and flexibility into business models and rethink global supply chains and relationships. At the same time, pressure is mounting to incorporate ESG principles into operational decision making. AI, data science, digital twins and sensing, monitoring and vision technology will all be essential to developing automation and control solutions that can help the manufacturing industry adapt to this new reality. In this context, I would like to share the top six trends that will impact and shape industrial automation in 2024 and beyond.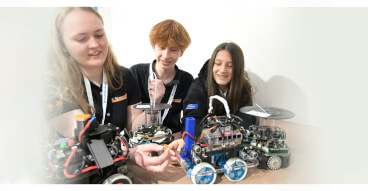
Empowering the workforce: OMRON's approach to skills development in European manufacturing
06 September, 2023 Delving into OMRON's unwavering commitment to nurturing skills that empower the next generation, while the industry embarks on a transformative journey – a journey that unlocks the full potential of the Fourth Industrial Revolution (4IR) while boldly moving towards the Fifth Industrial Revolution (5IR).In the halls of academia, the boardrooms of visionary business leaders, and the chambers of forward-thinking politicians, a fervent debate evokes. It revolves around the profound shift from the Fourth Industrial Revolution, 4IR, or Industry 4.0 as it is also known, to Industry 5.0 will change the world in which we live.Historically the Industrial Revolution was the First Machine Age, and electricity the Second, then electronics was the Third, and the internet as platform the Fourth Machine Age. We are now entering the Fifth Machine Age, which highlights harmonious human-machine collaboration and the contributions of the industry to society. This is the moment to not only adapt but to lead, to pioneer, and to create a future where innovation knows no bounds. Klaus Schwab, the founder and executive chairman of the World Economic Forum has observed that: “We stand on the brink of a technological revolution that will fundamentally alter the way we live, work, and relate to one another. In its scale, scope, and complexity, the transformation will be unlike anything humankind has experienced before. Our world is undergoing a transformative shift. Global production is evolving, driven by the automation of traditional industrial practices through smart technology, M2M communication, and IoT integration. This synergy fuels heightened automation, seamless communication, and intelligent machines that autonomously analyse and diagnose challenges.The rise of AI sparks debates, hinting at deeper transformations within our societal tapestry. As we navigate this dynamic landscape, we are poised to embrace innovation and reshape our future.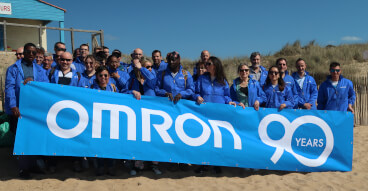
From red lights to robots: OMRON celebrates 90 years of innovation
06 June, 2023 This year on Founder’s Day, OMRON looked back on 90 years of pushing technological boundaries, and looks forward to a future of automation innovation framed by sustainability, digitalisation and human-machine collaboration.May the 10th be with you… Every year, 10th May is probably the most important day in OMRON’s calendar. On this day, 30,000 OMRON employees around the world celebrate the life and legacy of the company’s founder, Kazuma Tateishi. They do this by recommitting to Tateishi’s vision of using technology to create a better world and by giving back to society - often by participating in volunteer and charity projects in their communities. Innovation Milestones OMRON's journey of innovation began in 1933 with the development of a high-precision timer for X-ray photography. This marked the company's first contribution to addressing societal needs. In 1960, OMRON unveiled the world's first non-contact proximity switch, revolutionizing advanced mass production capabilities. Since then, OMRON has continued to introduce groundbreaking technologies, including the first automatic traffic signal, unmanned train station system, wearable blood pressure controller, ultra-high-speed fuzzy logical controller, and automatic cancer cell diagnostic equipment.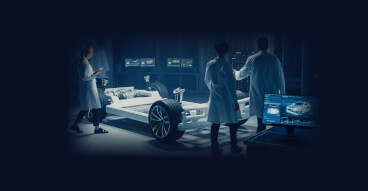
Why automated inspection systems are critical for electric vehicle manufacturing
23 March, 2023 Safety trumps all other concerns in the automotive industry, and electric vehicle manufacturing is no exception. However, safety can also introduce complexity, and the complexity of today’s vehicles – particularly EVs – is such that manufacturers are no longer able to rely on traditional sample or audit-based inspection methods.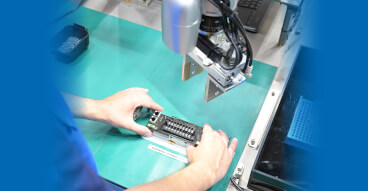
Top 5 automation predictions for 2023 from OMRON Europe
01 February, 2023 While a new year is upon us, with all its opportunities, I'd like to highlight some of the top trends that will impact and shape industrial automation in 2023 and beyond. The manufacturing industries will continue to face many challenges, and riding them out will involve building resilience and flexibility into business models. At the same time, companies must embrace emerging technologies - sensing, robotics, 5G and artificial intelligence - to help them solve the problems they face due to societal challenges.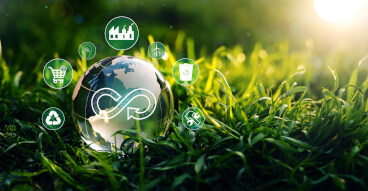
The path to net zero: talking tactics
01 February, 2023 The key to unlocking a net zero future in manufacturing is transforming the value chain through automation.In June 2022, New Scientist reported that a third of the world’s largest companies had net zero targets - significantly more than the same time last year.Whilst it is positive news that momentum is accelerating, the article went on to say that the details of how companies were planning to reach net zero were patchy.Which is not surprising really. Creating and implementing a net zero strategy is a huge undertaking for any business, especially with 80% of GHG emissions falling into Scope 3 - that is emissions that occur upstream or downstream in the value chain. This is a particular challenge for FMCG companies, whose supply chains and onward logistics are long and complex.Most of these businesses know what they need to do: decarbonise and circularise the value chain. And they have a strategy for doing this, which will generally cover: optimising the use of resources and energy, replacing high emission products and processes and eliminating waste.But translating intention into action is where the main challenge lies. This is where automation has a crucial role to play.Data collection and analysis is the key to successful net zero transition. Without it, how do companies know what their starting point is, where they need to improve, whether they have improved and by how much? Robust data is the foundation for turning a commitment into change, and for credibly and confidently communicating with stakeholders and delivering on climate ambitions.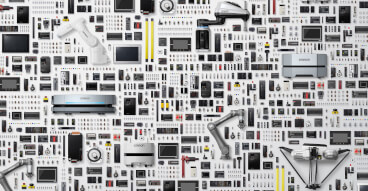
Riders of the storm: navigating economic uncertainty by turning social challenges into tech opportunities
06 December, 2022 One of the questions I am often asked is what our strategy is, as an industrial automation business, for maintaining stable growth in a volatile and increasingly unpredictable global economy. My answer, as you might imagine, is not one sentence, although it is rooted in one concept: SINIC. SINIC stands for ‘Seed-Innovation to Need-Impetus Cyclic Evolution’ and is a theory that was developed by OMRON's founder, Dr. Kazuma Tateisi, in 1970. According to this philosophy, science, technology and society share a cyclical relationship, mutually impacting and influencing each other. Scientific breakthroughs help society to advance and social needs spur on technological development. OMRON Europe has always followed this philosophy, and has spent the last decade laying the foundations for creating value-adding solutions to present day social and economic challenges.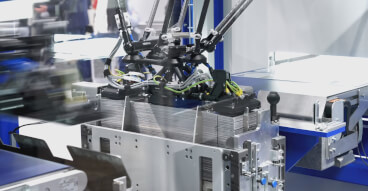
Digitalization in the automotive industry: Seven tips for smart production
02 November, 2022 If you want to grow and master crises, you have to be digitally fit – this also applies to the important automotive sector. There is no way around digital tools for addressing customers or productivity. Artificial intelligence (AI) and sustainability are key drivers and focus topics, as a study by Capgemini shows. Experts from Gartner point out the importance of open-source collaboration approaches, holistic ecosystems, and technology partnerships. But what should we look out for in digitalization and intralogistics in the production of the future? We want to answer this question in two parts. We start with tips on digitization in the smart factory. As an automation expert, OMRON has been accompanying manufacturers and suppliers on their way to more digitalization sophistication for many years.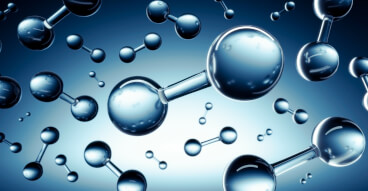